Industrial
Highlights
Scroll below the selected highlights for the full set of indicators.
Double Economic Output
The industrial sector halved energy intensity from 1977 to 2021, while more than doubling economic output.
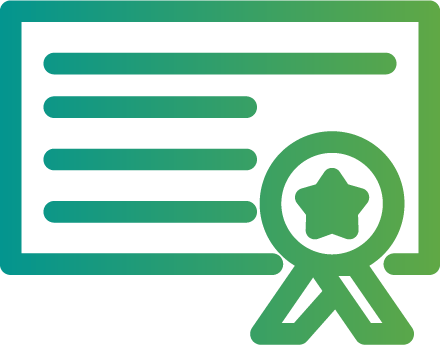
Industrial Energy Programs
Programs such as Better Plants and ENERGY STAR® for industry have led to higher levels of facility certification and nearly 5 quads of primary energy savings.
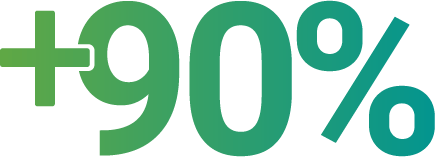
Industrial Energy Management
22% of manufacturers said that energy consumption is becoming a higher priority for the establishment and over 90% said energy efficiency is part of their purchasing decisions.
39
Industrial Energy Intensity
Industrial energy intensity has halved since 1970, while driving economic gains
Source: EIA (2021), Total Energy Monthly
DETAILS
The U.S. industrial sector consumes more total energy than any other end-use sector, and is responsible for 24% of total U.S. greenhouse gas emissions.1 It was also responsible for slightly more than 23% of the U.S. gross domestic product in 2021.2 As a result, this sector is a natural space to invest in energy efficiency; from 1980 to 2021, the industry halved energy intensity, while more than doubling value added. Energy efficiency contributed to this trend, with the deployment of innovative industrial processes, smart manufacturing, strategic energy management, and other strategies.3
40
Industrial Carbon Intensity
Industrial carbon intensity has declined 70% since 1980
Source: EIA (2021), Total Energy Monthly
Source: EIA (2021)
DETAILS
The carbon intensity (carbon emissions per value of output) from the industrial sector has steadily declined over the last five decades. Between 1980 and 2021, industrial carbon intensity has fallen by 70%. This decline is due to various factors, including energy efficiency, a shift to producing higher-value goods, and changes in energy source. However, this progress has slowed in the last decade or so.
Manufacturing makes up roughly 80% of industrial emissions, while non-manufacturing subsectors of construction, mining, and agriculture make up the balance of industrial emissions.
41
Combined Heat And Power
The industrial sector has largely driven CHP investments, a tool to enhance energy efficiency; commercial installations have significant potential
Source: DOE (2021) ; DOE (2016), Combined Heat and Power Technical Potential in the United States
Source: DOE/ICF (2020), CHP Installation Database
DETAILS
Combined heat and power (CHP) technologies are accompanied by significant efficiency gains: where separate systems to provide heat and electricity may reach 50% energy efficiency, CHP can often reach 75% efficiency. Most CHP installations are used for industrial applications, such as chemicals, refining, paper, primary metals, food processing, and other industrial processes, and natural gas is the most common CHP fuel, accounting for approximately 70% of U.S. CHP capacity in 2021.4, 5, 6 However, a wide variety of other commercial institutions are estimated to have significant untapped technical potential, collectively adding up to over 30 GW of potential capacity. 7 The total electrical capacity of CHP generation has remained largely constant from 2009 to 2020, though the number of sites has increased by approximately 27% over the same time period, largely driven by minor decreases in larger industrial installations, and increases in smaller commercial installations.
42
Industrial Energy Management
Over 131,000 manufacturing establishments use energy efficiency as part of their purchasing decision
Sources: LBNL (2022)
DETAILS
Industry accounts for more than 25% of U.S. energy use and greenhouse gas (GHG) emissions. Reducing this energy use through proven, cost-effective energy management techniques will improve the competitiveness of firms, helping maintain well-paying jobs in manufacturing. In order to reach long-term GHG reduction goals, it is vital that industrial emissions decline significantly. Energy management can deliver near- and longer-term reductions with low capital cost and can provide a host of energy and non-energy benefits.
While over 131,000 manufacturing establishments use energy efficiency as part of their purchasing decisions, fewer have taken specific steps to improve efficiency, such as establishing baseline energy use, conducting audits to identify opportunities, or setting energy consumption goals. However, nearly 20% of establishments identified that energy consumption is becoming a higher priority. ENERGY STAR® is the most common program for those who participate in some sort of energy management program.
43
ISO 50001
Facilities that have been certified to ISO 50001 demonstrate improved energy performance
Sources: ISO Certified – ISO (2022), The ISO Survey
DETAILS
ISO 50001 is an internationally recognized voluntary standard to support continuously-improving energy performance. DOE’s 50001 Ready is a simpler, self-guided energy management program. Facilities that have been certified to ISO 50001 and can demonstrate improved energy performance are eligible to be certified to DOE’s Superior Energy Performance (SEP) program. SEP-certified facilities have improved energy performance 4.6% annually, on average, through mostly (75%) no/low cost operational improvements.8 While the early adopters of ISO 50001 are realizing significant savings, there is enormous market potential for ISO 50001 to grow. Internationally, it is estimated that full ISO 50001 implementation could drive a cumulative energy savings of 59 quads, over $600 billion in energy costs, and avoid 6,500 Mt of carbon dioxide emissions to 2030.9
44
Better Plants
Better Plants participants make up 14% of the U.S. manufacturing footprint and have cumulatively saved 1.9 quads since 2011
Source: DOE (2022), Better Plants Program Information
Source: DOE (2022), Better Plants Program Information
DETAILS
The Better Plants Program’s 250+ partners make up 14% of the U.S. manufacturing energy footprint, span a diverse set of subsectors, and have already saved a cumulative 1.9 quads since the program’s inception.10 The number of Better Plants participants has steadily increased since 2014, with a slower growth as a share of manufacturing energy footprint.
45
ENERGY STAR® in Industry
The ENERGY STAR® program for industrial plants saved $2 billion in energy costs in 2020
Source: DOE (2022)
Source: DOE (2022)
DETAILS
In 2020 alone, the ENERGY STAR® program for industrial plants helped businesses save 30 billion kilowatt-hours of electricity (roughly 3% of all industrial electric use in that year),11 avoid $2 billion in energy costs, and achieve 30 million metric tons of greenhouse gas reductions by partnering with hundreds of companies to deploy ENERGY STAR® strategic energy management (SEM) resources to develop an organizational culture on continuous improvement of energy performance. EPA has convened 33 “Industrial Sector Focuses” to collaborate and develop industry-specific resources. Between 2000 and 2021, associated cumulative savings were 417 TWh of electricity and more than 4 quads of primary fuel savings.
ENERGY STAR® will continue to deliver industrial savings. In 2021, 93 new plants earned the ENERGY STAR® certification—earning above an ENERGY STAR® score of 75 out of 100—and another 28 industrial plants committed to reduce their energy use by 10% over 5 years.12
Footnotes
- EPA (2020), Sources of Greenhouse Gas Emissions
- BEA (2022) Interactive Data
- ACEEE (2017), Energy efficiency and industry: the national trend
- DOE (2019), Combined Heat and Power Basics
- EPA (2019), What Is CHP?
- DOE (2021), CHP Database
- The “Other Industrial” includes an aggregate of smaller-capacity categories of industrial facilities, including Agriculture, Mining, Oil/Gas Extraction and all other facilities listed in Table III-3 of DOE’s 2016 report titled “Combined Heat and Power Technical Potential in the United States.” The “Other Comm./Inst.” bar shown above includes an aggregate of smaller-capacity categories of commercial facilities, including Utilities, Unknown and all other facilities (aside from Comm. Buildings, Colleges/Univ., District Energy, Hospitals/Healthcare, and Multi-Family, which are separately shown in the chart) listed in Table III-4 of the DOE 2016 report.
- Paul Scheihing (2019), Presentation: Accelerating Energy Savings with ISO 50001
- LBNL (2016), Global Impact Estimation of ISO 50001 Energy Management System for Industrial and Service Sectors
- DOE (2021), Better Plant Program Information
- EIA (2021), Electricity Explained
- EPA (2022), About Energy Star for Industrial Plants
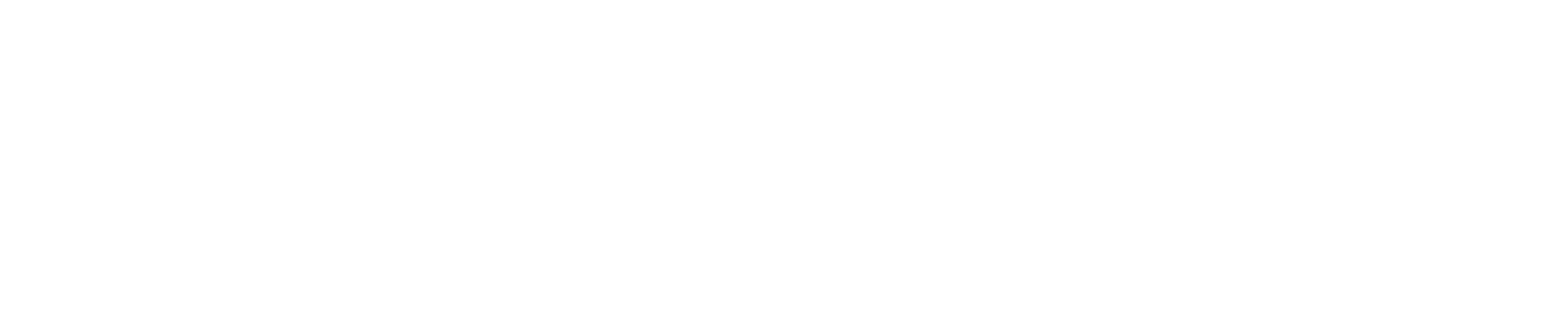